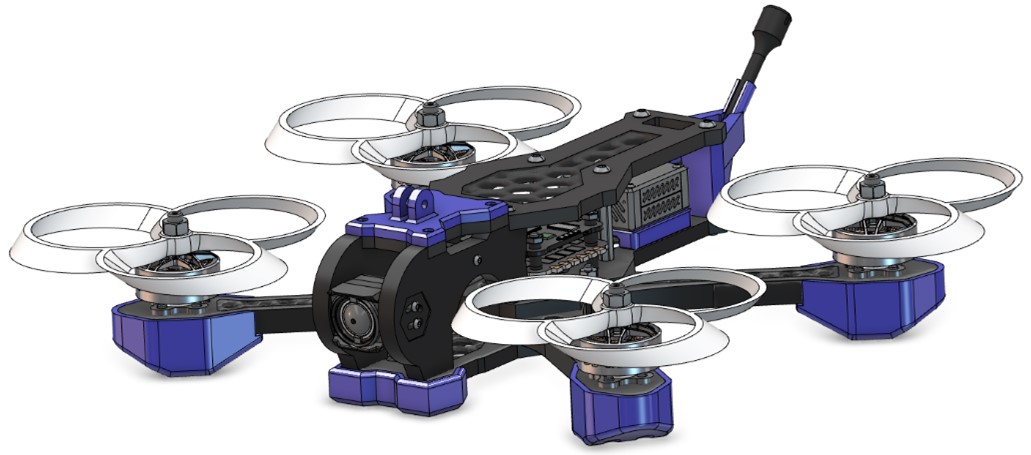
• End-to-End Development: Managed the complete design and development of a custom FPV (first-Person View) drone, transitioning from conceptual design to real-world flight within a tight 2-month deadline
• Internship Project: Undertook this comprehensive drone project during my second summer internship with the SOLIDWORKS Product Management team, modeling it in xDesign, their cloud CAD solution, contributing a complex native data set used for marking and product demonstration purposes
• Fast Learning: Went from knowing little about drones to designing, building, and flying my own custom FPV drone in just two months, showcasing quick learning for a complex, multifaceted project
• Creative Design and Problem-Solving: Utilized FDM 3D printing to create an intricate frame design, went through various design iterations and overcame numerous challenges, proving resilience, creativity, and real-world engineering skills
• Efficient Project Management: Delivered a fully functional drone model under tight deadlines, balancing a steep learning curve with effective time management and dedication to quality
Completed CAD Assembly
Final Assembled Model
• Efficient CAD Modeling: Leveraged the advantages of a single modeling environment for streamlined, top-down assembly approach, crucial for managing the drone’s large complex assembly design
• Design, Testing, and Iteration: Utilized 3D printing for rapid prototyping and numerous design iterations - especially the custom toroidal propellers - through the flexible single modeling environment, leading to successful outcomes after multiple iterations
• Soldering Skills: Entered the project with no prior soldering experience; quickly learned and applied soldering techniques essential for assembling the drone’s electrical components, ensuring secure and efficient connections vital for the drone’s performance
• Navigating the Learning Curve: Tackled a steep learning curve that involved extensive research into drone fundamentals, components consideration and compatibility, forming a comprehensive bill of materials essential for the subsequent design phase
• Initial Frame Design: Overcame the absence of physical components by extensively researching and sourcing design drawings for each part, ensuring the drone frame design was accurate and functional
• Balancing Design and Assembly: Managed a demanding schedule between detailed CAD modeling – including every minor component like fasteners, electrical hardware, wiring – and the physical assembly of the drone, showcasing effective multitasking and precision
• Learning Flight Control: Dedicated numerous hours to training in drone simulations, preparing for the real-world challenge of controlling a FPV drone, persisting despite several setbacks from crashes and broken components, a journey which highlights resilience and the ongoing commitment to skill development
• Successful Project Completion: Achieved the significant milestone of getting the drone airborne before the internship’s conclusion, a feat showcased to the CEO of SOLIDWORKS, highlighting the project’s success
• Comprehensive Engineering Process: Managed a complete end-to-end engineering design process for the first time, handling everything from initial research to final testing, understanding the intricacies involved in bringing a complex project to fruition
• Emphasis on Design Intent: Learned the importance of detailed design intent, focusing on manufacturability and ease of assembly in design, understanding the importance of creating models that translate efficiently from screen to reality
• Streamlined Assembly and Hardware: Realized the benefits of designing for simplified assembly and incorporating uniform hardware, making both construction and part replacement more efficient while optimizing cost and resource management
• SOLIDWORKS Blog Feature: Authored an in-depth blog post detailing the journey and insights gained throughout the drone project, providing a narrative on the design and manufacturing process. Explore the full story here: View Blog Post
Additional Images of CAD Model and the Final Assembled Drone in its Physical Form